物流センター・自社倉庫・製造工場をお持ちのご担当者さま
このような課題はございませんか?
ピッキングミスを防止し、誤出荷ゼロを目指したい
作業者の人数を増やすことが難しく、1人あたりの生産性のUP、在庫管理の精度を上げたい
物量や時期に合わせて倉庫内の好きな場所で仕分け作業を行いたい
作業者の入れ替わりに左右されないピッキングの精度とスピードを向上させたい
商品が多種多様で、大きさ・重さ・注文数がまちまちなため、柔軟に対応できるシステムを検討している
デジタルピッキングシステム(DPS)とは
デジタルピッキングシステム(DPS)とは、表示器を利用したピッキング支援システムです。
ピッキング支援システムを導入することで、出荷ミス・ピッキングミスを軽減し、これまで時間がかかっていたピッキング・仕分け作業の
効率化・スピードアップを可能にします。工場現場での省人化・生産性改善といった物流と製造業の生産性改善を実現します。
【物流センター・自社倉庫・製造工場の生産性を向上】
システムを導入することで誰でも簡単に作業ができます。プロジェクションピッキングシステムⓇ(PPS)はプロジェクターを使い、従来の表示器設置が困難だった場所でもピッキング作業を可能にしました。
デジタルピッキング:表示器(有線・無線)の仕組み
デジタルピッキング表示器とは、ランプ動作・数字表示・音でピッキング対象を知らせる仕組みです。
工場や物流センターの作業者は、表示器のランプが光った場所に足を運び、表示された数だけ商品を取り出します。下図のように表示器の指示に従って行うピッキング作業は、正確かつスピーディーなピッキング作業を実現します。
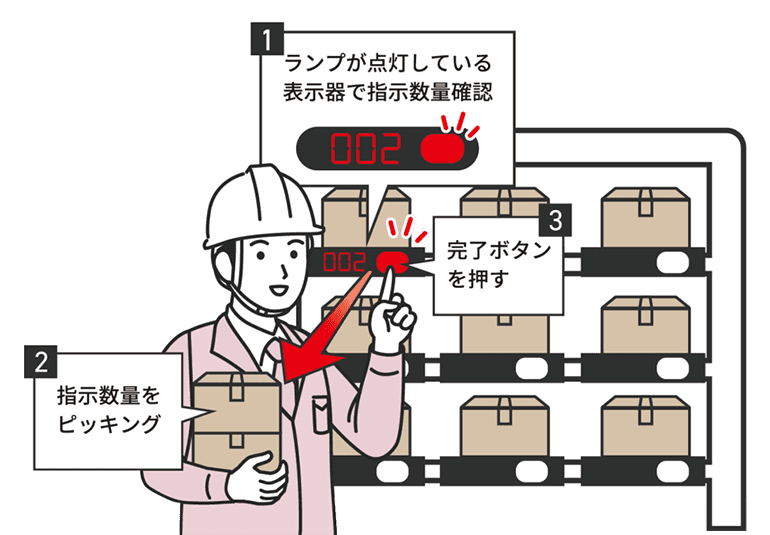
デジタルピッキング表示器ラインナップ
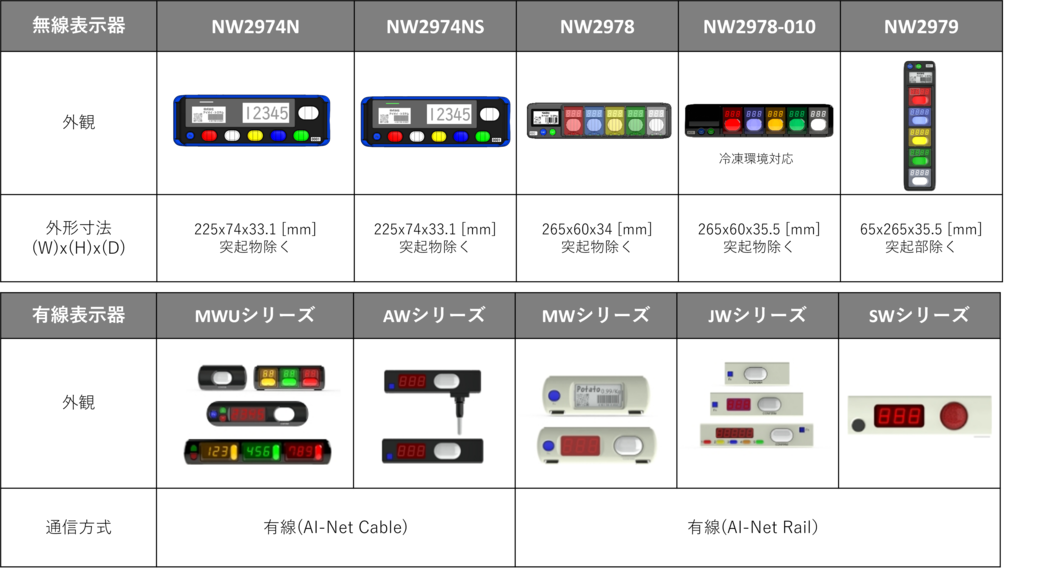
さまざまなデジタルピッキングシステム
TOPPANではご要望に合わせて最適に活用いただけるよう、さまざまなデジタルピッキングシステムをご用意しております。
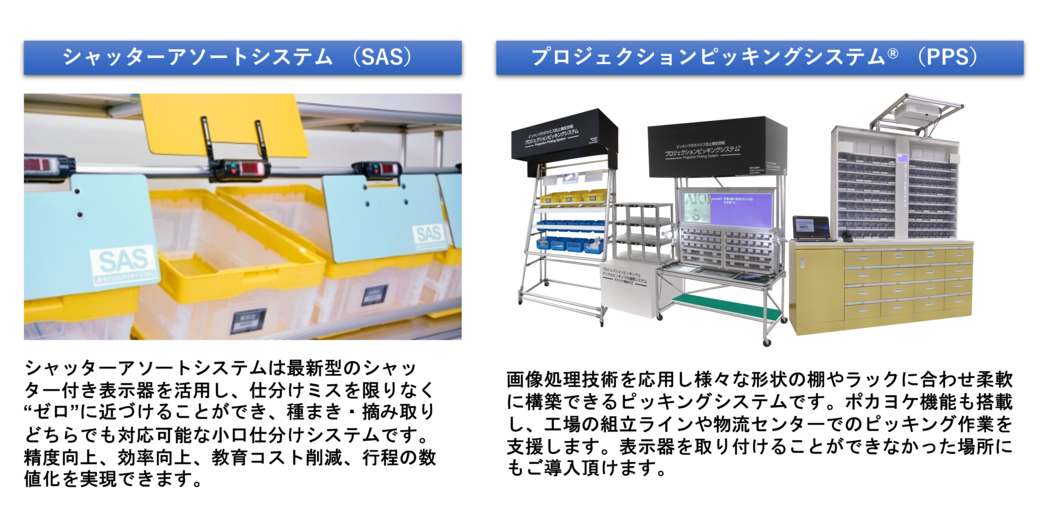
プロジェクションピッキングシステム®(PPS)
プロジェクターを使い、従来の表示器の設置が困難だった様々な形状の棚やラック、床面や壁面にも画像、文字、数字、QRコードなどを直接投影できるピッキングシステムです。画像認識、センサー認識(2D・3D)など、
現場の環境に合わせた様々なポカヨケ機能が搭載可能です。
プロジェクションピッキングシステム®は工場の組立ラインや物流センターでのピッキングや仕分け作業に活用されています。
動画にて詳しくご説明しています。画像下のテキストリンクをクリックください。
【このようなシーンでご活用いただけます】
・FA現場で重要保安部品等を管理
・仕分けしておりミスが許されない現場
・医薬品を扱う現場
・ピッキング以外にも組立て作業等の別工程も支援
・作業者にとって視覚的に作業がしやすい多言語対応等画期的なシステムを探している
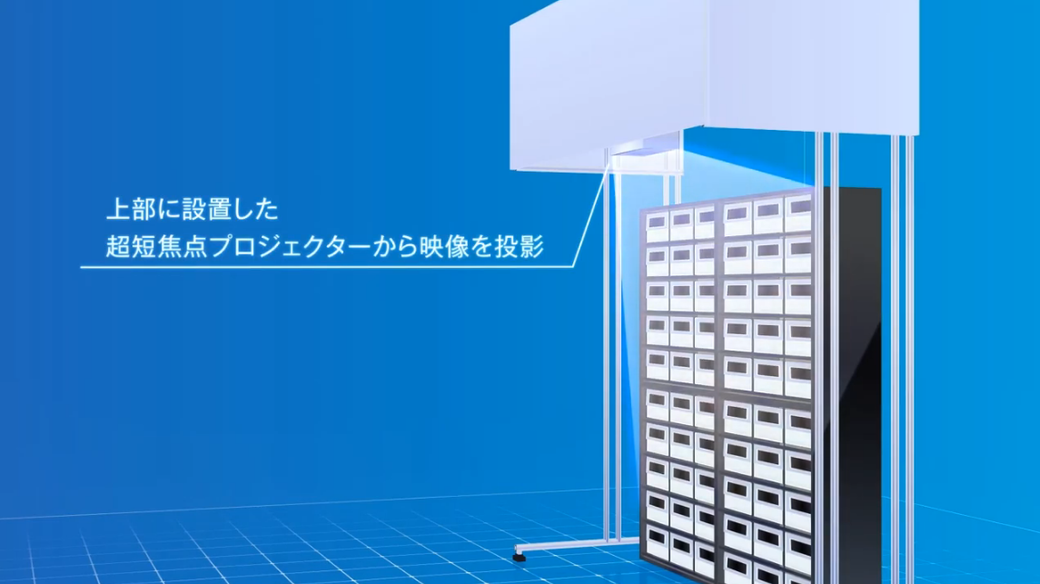
シャッターアソートシステム(SAS)
シャッターアソートシステム(SAS)は最新型のシャッター付き表示器(ポカヨケゲート表示器)を使用したデジタルピッキングシステムです。使い方はとってもシンプル。対象のバーコードをスキャンし、開いたところに指示数の商品を投入、投入完了ボタンでシャッターが閉まります。トレーニングに時間を費やすことなく、導入後すぐにお使いいただけます。
eコマースや店舗仕分けにも最適なシステムです。動画にて詳しくご説明しています。画像下のテキストリンクをクリックください。
【このようなシーンで活用いただけます】
・FA現場で重要保安部品等を管理、仕分けしておりミスが許されない現場
・医薬品を扱う現場
・荷主、売主、ユーザーの要求精度が高い
・検品レスで業務効率を改善したい
・作業者にとって視覚的に作業がしやすい画期的なシステムを探している
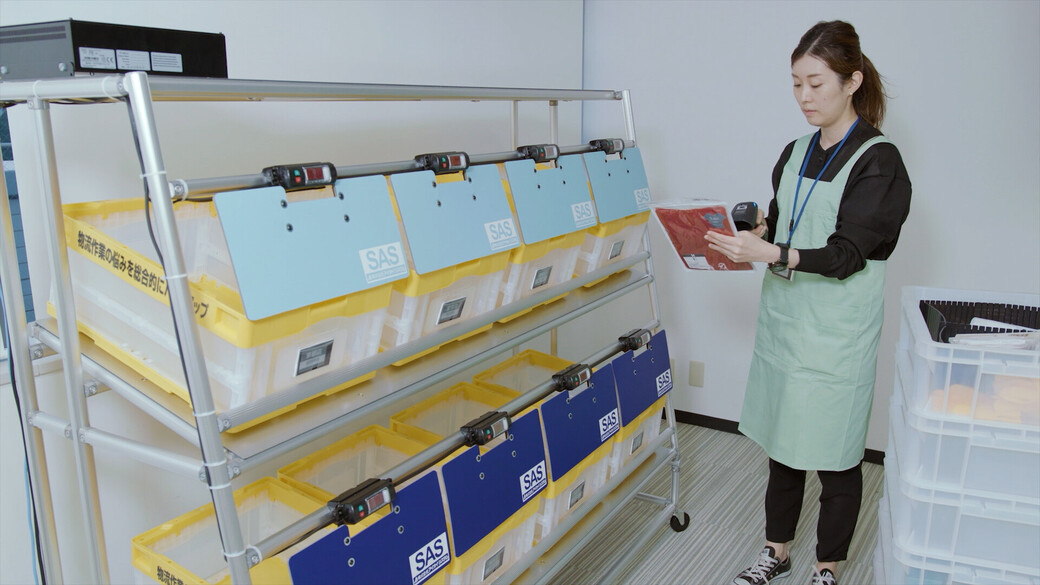
デジタルピッキングシステムの導入事例
取り扱い品目・作業方法に応じたデジタルピッキングシステムを、様々な業界に導入いただいております。
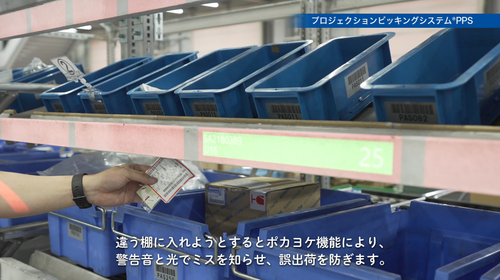
メンテナンス部品仕分けの効率化で 「修理を長引かせず、工事現場を止めない」を実現
センサー方式のプロジェクションピッキングシステム®(PPS)導入により、仕分け作業の簡易化が実現され、作業者による作業スピードのバラつきがなくなり、作業を標準化することで、仕分け業務の生産性がアップ。
さらにポカヨケ機能により、作業者が入れた手の位置を検知し、警告音と光でミスを知らせ、仕分けミスが激減しました。
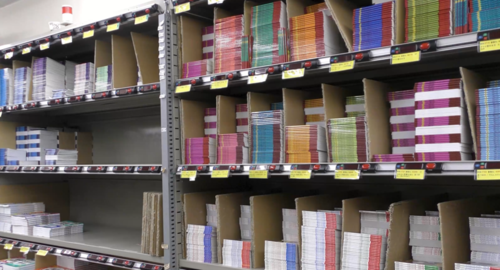
生産性が約1.5~約2.0倍に向上
ピッキング作業の効率化のため、デジタルピッキング表示器約1,600台を導入頂き、熟練作業者に属人化していた作業を標準化。
作業負荷軽減・作業品質の向上に成功し、ご満足頂いております。
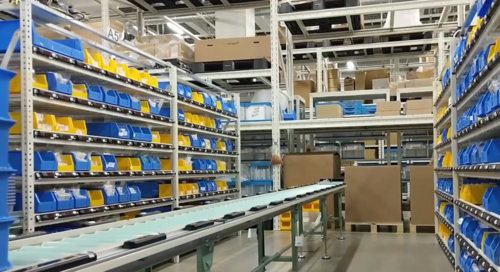
複雑化する複数種類の仕分けを誰でも簡単に!
医療機器のピッキングと仕分けを行う作業現場で、表示器の指示に従い作業を行うシンプルな仕組みを導入頂きました。
作業者に優しく、誰でも簡単にできる仕分けシステムを実現。その結果、作業効率17%アップ、作業人員の削減に成功されました。
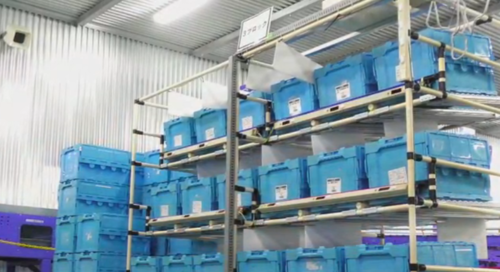
入れ間違い防止付移動式ラックで、ミス防止とスペース有効活用に成功
病院や工場の食堂向けに商品を発送しているムロオ様では、上下左右の入れ間違い防止が付いた移動式ラックを導入頂きました。
入れ間違いミスによる誤出荷の削減、物量や繁閑期に応じたラックの移動による倉庫内のスペース有効活用に貢献しました。
デジタルピッキングシステム導入のメリット
- 1
- 作業精度の向上(精度 約10倍)
初心者や高齢者や外国人も合わせた熟練度の低い作業者でも、間違いのない迅速な作業が簡単な説明だけででき、教育にかかる負担を軽減することができます。またピッキングリストも不要になり、書面等のペーパーレスが実現します。
初心者や高齢者や外国人も合わせた熟練度の低い作業者でも、間違いのない迅速な作業が簡単な説明だけででき、教育にかかる負担を軽減することができます。またピッキングリストも不要になり、書面等のペーパーレスが実現します。
- 2
- 作業時間の短縮(作業スピード 約2倍以上)
仕分けが多くてもわかりやすく指示をサポート表示。そのことで作業効率があがります。最短距離で該当アイテムへ導いてくれるため作業時間を短縮し、作業スピードを約2倍以上に向上させます。
仕分けが多くてもわかりやすく指示をサポート表示。そのことで作業効率があがります。最短距離で該当アイテムへ導いてくれるため作業時間を短縮し、作業スピードを約2倍以上に向上させます。
- 3
- 作業実績の可視化 いつ・だれが・どのようなピッキング作業を実施したのかが可視化でき、作業実績をトレースできます。
いつ・だれが・どのようなピッキング作業を実施したのかが可視化でき、作業実績をトレースできます。
ショールームのご案内
製品の使い勝手と機能性を実感いただけるよう、東京・大阪にショールームを設置しています。
ショールームでは、各種ピッキングシステムをはじめ、
様々なソリューションをご紹介いたします。
■展示内容(時期によって変更します)
❶各種デジタル表示器(無線/有線モデル、冷凍、チルド、常温、高温対応モデルなど)
❷シャッター付きピッキングシステム (SAS)
❸AGV(自動搬送車)+ PPS + SASによる世界初のピッキング・仕分け連動システム
❹電池レスの電子ペーパー付RFIDカード スマートカードによるUHF一括読込、HF一括書換
❺無線一括書換 電子棚札ソリューション
❻構内設備一括コントロール Smart AI
TOPPANはショールームをお客さまとつながる『コミュニケーションの場』として活用しています。ショールームで、製品の使い勝手と機能性を実感してください。
見学のご予約はお問い合わせフォームよりお願いいたします。
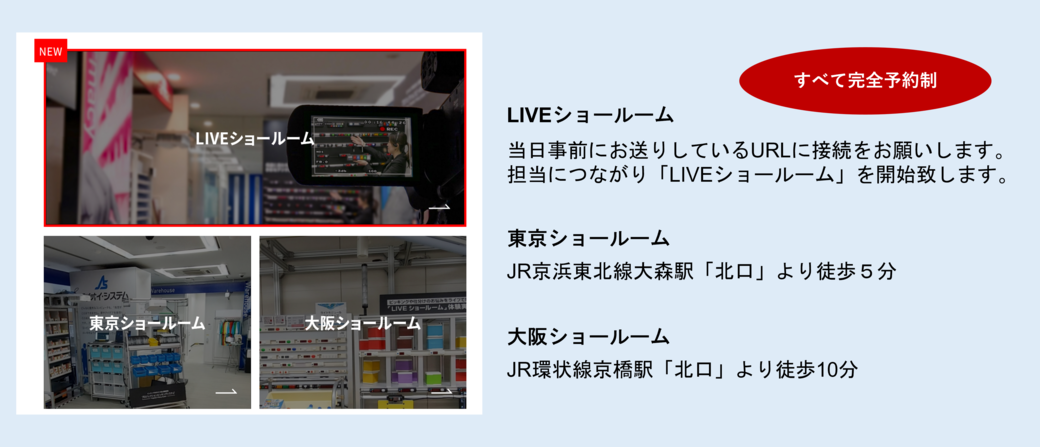
TOPPANの物流・製造DXソリューションの強み
-
メリット❶システム導入実績 さまざまな業界で導入いただきました。取扱品目・業界・作業方法に応じ、経験に基づくきめ細やかな提案力と運用支援が強みです。
-
メリット❷全国のTOPPAN 営業・担当者がコーディネート 全国のTOPPAN 営業・担当者がお客さまの工場へ赴き、お客さまの課題解決に直結するご提案をいたします。
-
メリット❸物流・製造現場のDX・ IoT 化をトータルでサポート デジタルピッキングシステムのご相談はもちろん、貴社の店舗・工場・倉庫全体の作業効率化のご提案やDX化のご相談全般を承ります。これまでの知見を活かした最適なご提案をいたします。
導入フロー・導入後サポート
お客さまのニーズ・利⽤⽤途に応じ、デバイスの手配からシステム導入、アフターサポートまでワンストップでサポートします。
-
STEP 1
初回お打ち合わせ
TOPPAN 担当者より現状課題、目的、内容、進め方、スケジュールなどをヒアリング致します。
-
STEP 2
ショールームご見学
アイオイ・システムの商材全般のご説明を致します。ショールーム での現地対応、もしくは オンライン対応のどちらでも対応可能です。
-
STEP 3
現地調査
現地にお伺いさせて頂き、ご提案に向けて調査致します。出荷伝票、実データなどの各種データを頂けると物流データ分析が可能です。
-
STEP 4
ご提案・概算費用提出
現地調査結果に基づいたご提案を実施致します。同時に概算費用のご提示も致します。
-
STEP 5
要件定義・御見積提出
ご要望に対して齟齬が無いように要件定義を致します。同時に詳細な費用感のご提示も致します。
-
STEP 6
ご導入
ご発注確定後、速やかに導入に向けて動きます。商材によっては配線関係の各種工事が発生する可能性もあります。
-
STEP 7
導入後サポート
導入後のアフターフォローも適宜、実施しております。ご契約内容に基づき、保守サービスもご提供させて頂きます。
よくある質問
ピッキングシステムをご発注いただく際に、よくいただく質問
-
製品や動きを実際に見れますか。
東京・大阪にショールームがございます。ご来社不要でオンライン(LIVEショールーム)でもご案内可能です。 お客さまの現場でデモンストレーションも可能です。
-
稼働している現場数はどれくらいですか。
世界中で10,000システム以上の実績があります。
-
導入先ユーザーの見学は可能ですか。
別途、秘密保持契約書を締結したうえでご見学可能です。
-
どのような現場に導入されていますか。
世界各国の食品・アパレル・医薬・量販店・eコマースなどの配送センターや自動車工場関係をはじめとする製造業など、様々な業界に導入されております。
-
テスト導入は可能ですか。
可能です。お気軽にお問い合わせください。
関連サービス
-
資産管理クラウドサービス「Convi.BASE(コンビベース)」
ICタグ・バーコードを活用してあらゆるモノの管理・棚卸しを効率化するクラウドサービスです。
-
資材管理システムBRIDGITAL®(ブリジタル)for order
資材の発注・在庫・配送管理のデジタル化で作業効率化と見える化を実現。
-
RFIDタグソリューション
RFIDタグ媒体の設計・開発はもちろん、最適なリーダライタの選定や運用設計、システム開発、導入支援までワンストップでご提案します。
-
物流データ可視化サービス「LOGINECT®データ可視化」
データの一元管理で物流業務を見える化し、効率的な意思決定をご支援するデータ可視化サービスです。