倉庫業務を効率化!
入庫・出庫・在庫管理の改善ポイント9選
物流倉庫の業務効率化を推進することで、物流コストの削減や生産性の向上が可能です。
しかし、一概に業務効率化といっても、さまざまな手法があるため、何から取り組むべきか悩んでいる方も多いのではないでしょうか。
そこで本記事では、倉庫業務を効率化するためのアイデアを9つ紹介します。ぜひ参考にしてください。
倉庫業務の効率化のアイデア
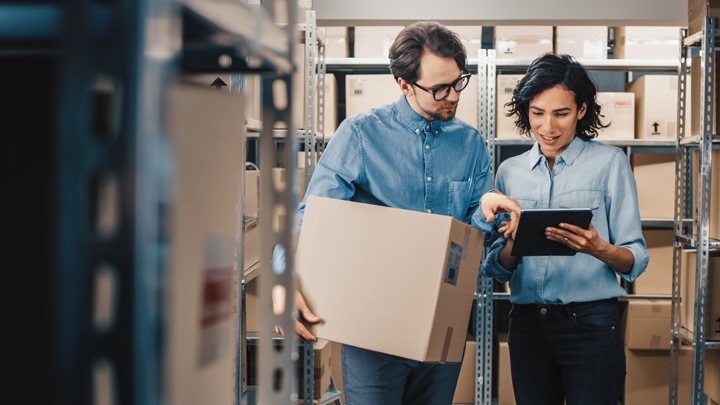
倉庫業務には、入出庫や在庫管理といった幅広い業務が含まれています。このような業務を効率化するためには、次の9つのアイデアを活用するのが効果的です。
● 倉庫内を整理整頓し作業効率を上げる
● 商品レイアウトを見直し移動時間を削減する
● 商品の種類に合わせて最適なピッキング方法を選ぶ
● ピッキングリストを作成し作業ミスを減らす
● 商品の入出荷時間の最適化し人員不足を回避する
● 業務マニュアルを作成し業務の標準化を図る
● 適正在庫を維持することで余計な作業をなくす
● RFIDで入出庫時の商品の読み取り作業を高速化する
● 在庫(倉庫)管理システムで在庫状況を把握する
倉庫内を整理整頓し作業効率を上げる
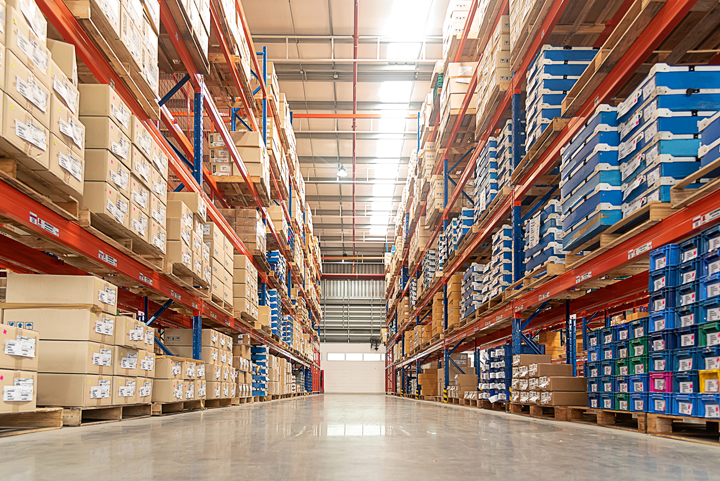
倉庫内に商品が無造作に置かれている状態では、作業効率が低下する可能性があります。作業に不要な物が多いほど、作業員の動線に乱れが生じるためです。また、作業場の整理整頓が行き届いていない状態は、安全性の観点からもおすすめはできません。
そのため、倉庫内を綺麗に整理し、スムーズに作業を行える動線を確保することが重要です。使用した道具は定位置に戻し、棚に入らない商品は仮置きスペースに保管しましょう。そのほか、搬送待ちの商品を荷捌きスペースに一時保管するなど、置き場所を固定するのも効果的な方法です。
商品レイアウトを見直し移動時間を削減する
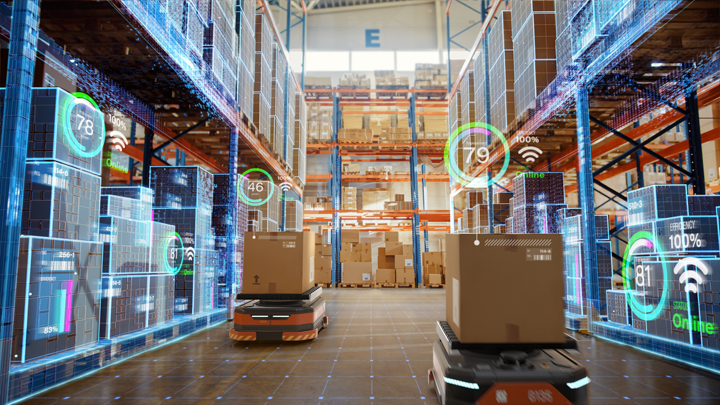
倉庫内では、出荷頻度に合わせて商品レイアウトを工夫すると、移動時間の削減につながります。そのためには、ABC分析を活用するのが効果的です。
ABC分析とは、出荷頻度ごとに商品をA・B・Cのランクに分ける分析手法です。Aランクに近い商品ほど回転率が高く、これらの商品を出入口付近にレイアウトするとピッキング効率が向上します。
なお、時期によって出荷頻度が異なる商品は、フリースペースに配置すると良いでしょう。
商品の種類に合わせて最適なピッキング方法を選ぶ
ピッキングには、「シングルピッキング」と「トータルピッキング」の2種類の方法があります。それぞれの特徴は次の通りです。
特徴 | 適しているケース | |
シングルピッキング | 1回のオーダーごとに商品をピッキングする方法 | 1オーダーあたりの商品種別が多い場合 |
トータルピッキング | 複数回のオーダーを一度にまとめてピッキングし、後でオーダーごとに分ける方法 | 1オーダーあたりの商品種別が少ない場合 |
最適なピッキング方法は、1オーダーあたりの商品種別や倉庫内の環境によって異なります。そのため、両者の特徴をよく理解したうえで、適切な方法を選択しましょう。ピッキング方法が最適化されると、業務効率化に寄与します。
ピッキングリストを作成し作業ミスを減らす
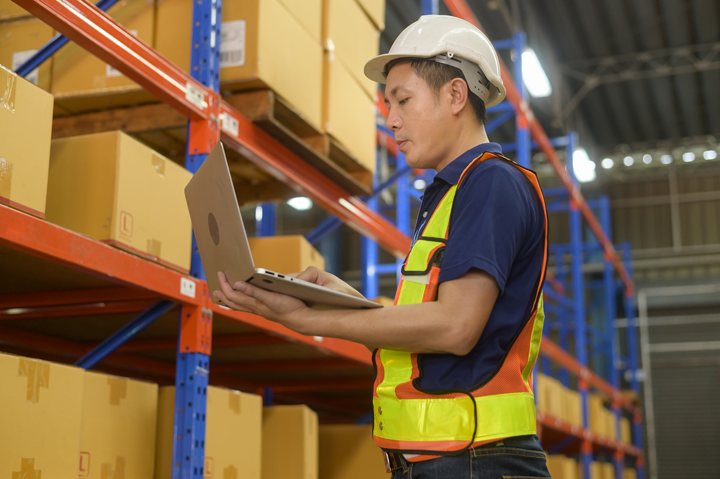
作業員が効率良くピッキングを行うには、専用のリストを作成することが重要です。
リストには、出荷する商品や数量、保管場所などの情報が記載されているため、作業ミスの削減や業務効率化につながります。 また、リストを作成すれば、作業に不慣れな作業員でも素早く目的の商品へとたどり着けるようになります。これにより、ピッキング作業の均質化が可能です。
更なる効率化やミスの低減をめざすなら、デジタルピッキングシステムの導入がおすすめです。
デジタルピッキングシステムを利用すれば、作業者はランプが光る場所に足を運び、表示されている数だけ商品を取り出すだけ。人為的なミスの防止はもちろん、作業の効率化を実現します。
商品の入出荷時間を最適化し人員不足を回避する
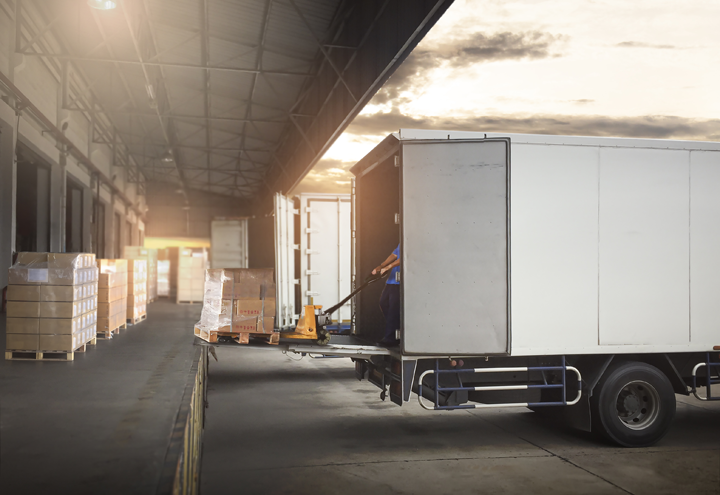
仕入先や出荷先が複数箇所に分散する場合は、入出荷のタイミングが重なり、作業効率が大幅に低下する可能性があります。作業員がそれぞれの入出荷位置に分散すると、人員不足に陥りやすいためです。
このような事態を避けるには、商品の入出荷時間が重複しないように調整することが大切です。
業務マニュアルを作成し業務の標準化を図る
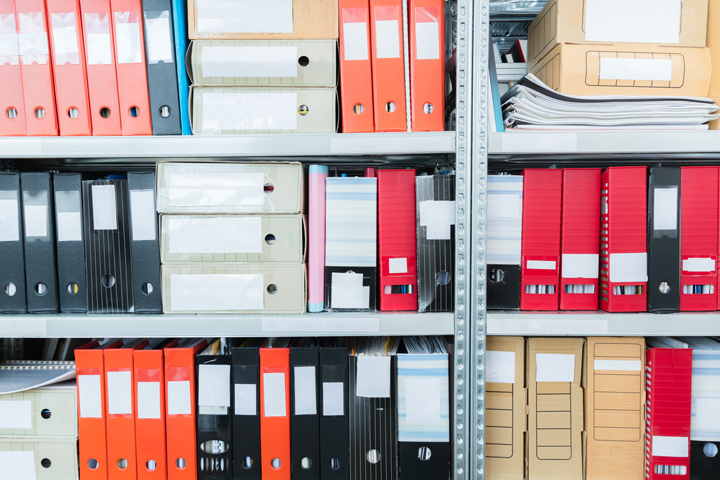
業務マニュアルは、業務の属人化やヒューマンエラーの予防などに効果を発揮します。
作業の進め方や機械の操作方法などを一つの書面にまとめておくと、誰が作業しても均一的な結果が得られます。また、わからないことがあれば、いつでも資料を参照できるため、確認不足によるミスや漏れのリスクを抑えられるのも利点です。
さらに業務効率化を図るには、モバイル端末に業務マニュアルを移行するのも一案です。デジタル技術を上手く活用すれば、紙に出力する手間を削減できるほか、動画を用いた理解促進が図れます。
適正在庫を維持することで余計な作業をなくす
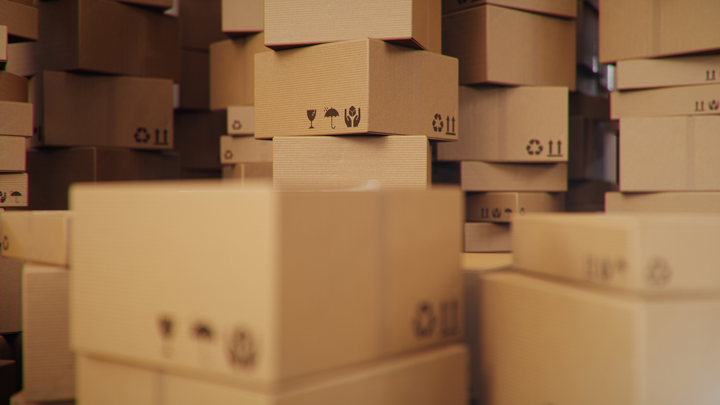
倉庫内で過剰在庫を抱えている場合、保管スペースを確保しなければならない点に加え、作業員の動線にも悪影響を与えます。反対に在庫数が少なすぎても、発注回数が増えて作業効率を損ねてしまうでしょう。
そのため、在庫数は多すぎず、少なすぎずの適量を意識することが重要です。入出庫のバランスや平均在庫数の推移などを参考に、在庫数の最適化を図りましょう。
RFIDで入出庫時や棚卸時の商品の読み取り作業を高速化する
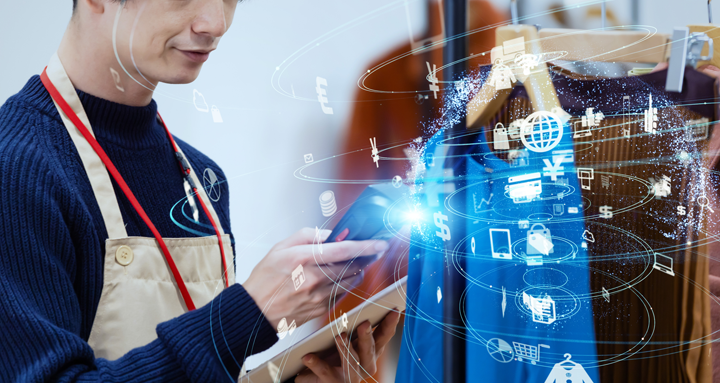
RFID(Radio Frequency Identification)とは、ICタグに紐付いたデータを、電波を用いて非接触で識別する技術です。複数の商品データを一括で読み取れるため、一つひとつの商品をスキャンする必要がありません。
RFIDには、用途や管理する商品やに合わせ、形状やサイズ、機能の違いなど様々な製品が用意されています。機能だけでなく導入費用にも違いが現れるため、倉庫の規模や商品数によって適切な種別を選択しましょう。
在庫(倉庫)管理システムで在庫状況を把握する

在庫管理システムとは、リアルタイムの在庫状況を一元管理するためのツールです。倉庫向けのツールは倉庫管理システムと呼ばれることもあり、在庫だけでなく入出荷や棚卸しなどの情報まで管理できます。
在庫管理システムでは、単に在庫数が可視化されるだけでなく、「どこに・どのような商品があるのか」といったロケーション管理が可能です。目視で在庫確認を行わずに済み、抜け・漏れなどのヒューマンエラーを避けられるため、業務効率化に効果を発揮します。
倉庫の業務効率化を実現したいならTOPPANへ!
倉庫業務の効率化を図るには、今回紹介したような、さまざまなアイデアが活用できます。単独の取り組みだけでなく、複数を組み合わせることで、業務効率化の効果が大きくなります。
数ある取り組みのなかでも、デジタル技術を活用した方法に興味がある方は、TOPPANが提供する「LOGINECT®データ可視化」を検討してみてはいかがでしょうか。
「LOGINECT®データ可視化」は、物流業務のあらゆるデータを収集・蓄積・分析できる物流業務支援システムです。適正在庫・商品レイアウトの分析による保管スペースの有効活用や、多頻度小口化する配送状況の可視化分析による配送効率の向上といった効果が期待できます。
以下で詳細を紹介していますので、ぜひ参考にしてください。
お客さまのビジネス変革と持続的な発展をサポートするため、
さまざまなデジタルソリューションを提供しています。
下記画像をクリックし、その他のソリューションもご覧ください。
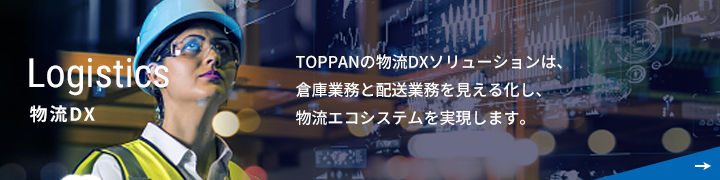
2024.05.23